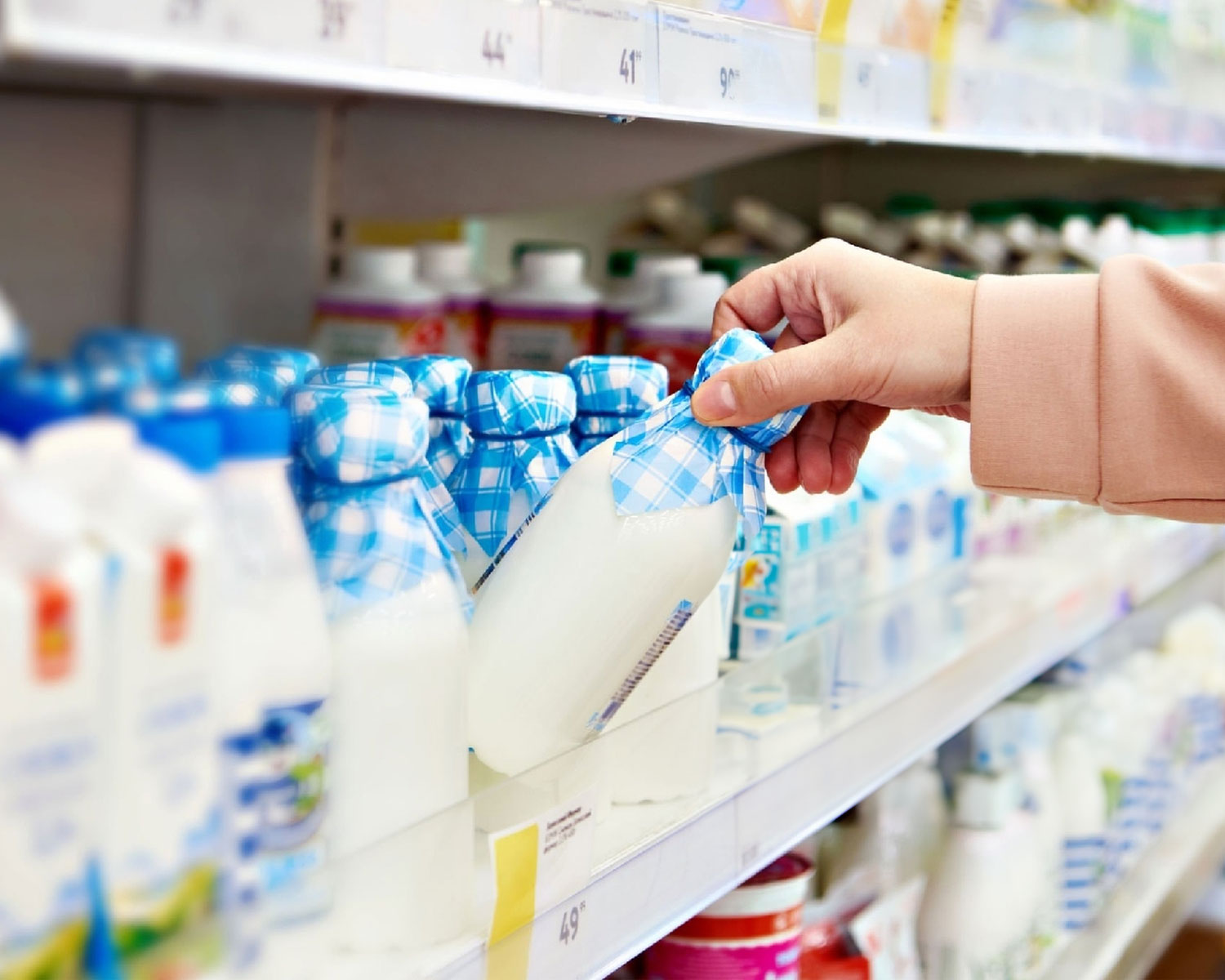
The Challenge
This leading dairy producer was looking to optimise energy consumption and asset utilisation in their retail outlets. In the dairy industry, maintaining strict temperature compliance is crucial for ensuring product quality and food safety. To achieve this, the company sought enhanced control and visibility over product temperature set points in their store freezers. This would enable better monitoring and management of product conditions, ensuring consistent quality and safety standards while enhancing operational efficiency and achieving cost savings.
Our Solution
Our initial energy consumption analysis revealed that the thermostat was operating at maximum capacity, relying on coil temperature for regulation and resulting in high energy consumption. We deployed our IoT-based AOne Edge devices to adjust the temperature according to ambient conditions, significantly reducing energy usage. Additionally, we automated defrost cycles based on calculated optimal intervals, enhancing compressor efficiency and further conserving energy.
We also assisted the client with precise temperature monitoring. Previously, the thermostat maintained temperature without accounting for ambient conditions. Our solution ensured asset temperatures remained between 20 and 22 degrees Celsius, optimising based on ambient temperature and reducing energy consumption.
Furthermore, we enabled predictive analytics capabilities to foresee and prevent unexpected asset downtimes. By optimising and continuously monitoring asset performance, we enhanced asset health, which will help extend the asset life cycle.
– Real-time temperature monitoring
– Maintenance of asset’s ambient temperature at required thresholds
– Automation of regulator control
– Facility-wide energy monitoring
– Asset-wise energy consumption analysis
– Predictive component health monitoring
– Real-time HVAC optimisation and remote control
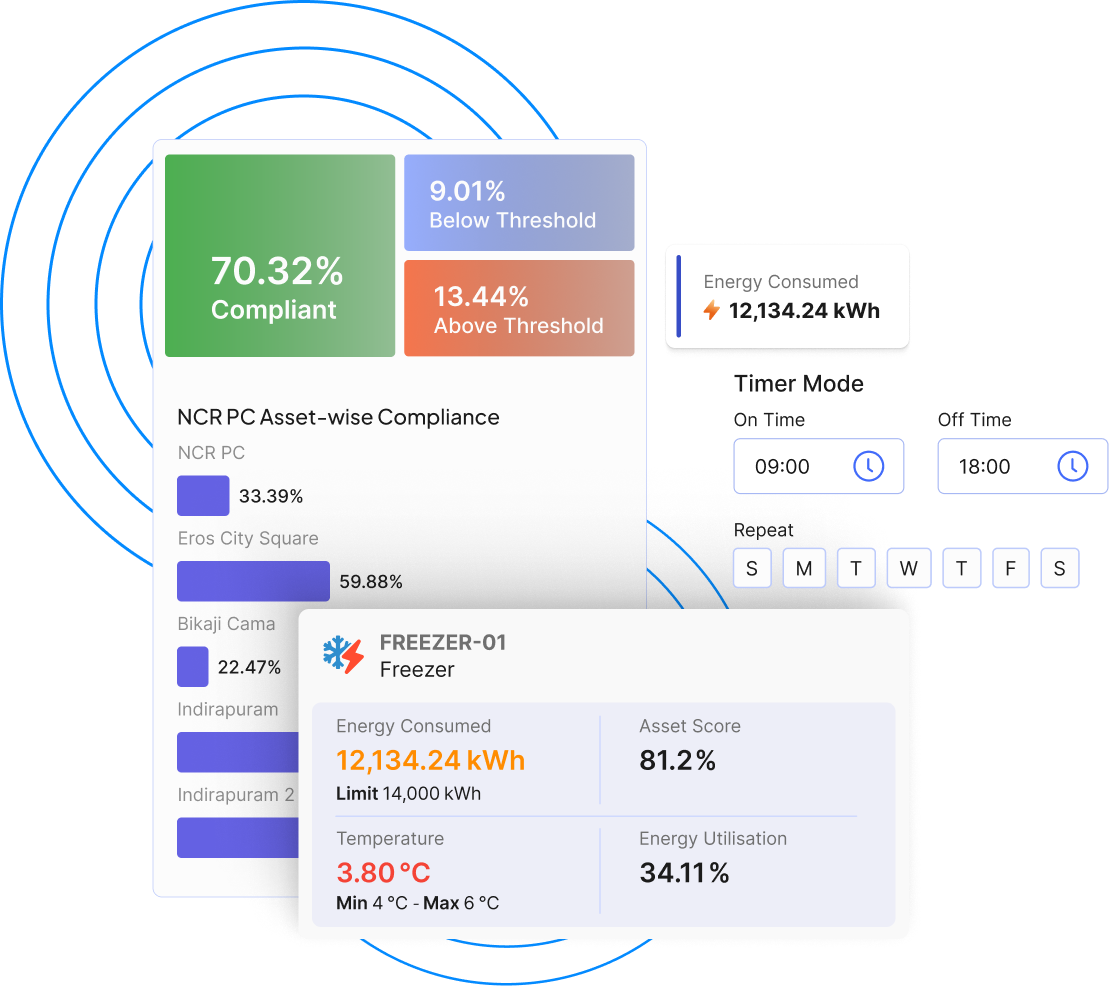